The filling line just got drastically smaller, significantly safer and potentially less expensive. The result is safer and less expensive drugs that will save countless lives.

NEW MILFORD – Something phenomenal is happening in the field of aseptic processing technology that’s putting one Connecticut research and development company on the world stage, and the mission is to make medicine affordable at the highest safety level to those in need.
For 26 years, Medical Instill Technologies (MEDinstill) – headquartered in New Milford at 201 Housatonic Avenue – has invented groundbreaking aseptic processing technology for companies in the pharmaceutical, biotech, healthcare, nutrition and cosmetics sectors.
Their clients, who manufacture some of the most recognizable products in the world, have one thing in common: all sterile liquid products must be sterile.
Oftentimes, it’s a matter of life or death for a sick patient in a hospital, or a wounded soldier out in the battlefield, who needs a medical injection to be sterile and free of organisms.

The company received state approval last year, a first step in the FDA 503B registration process.
“Our sterile INTACT Filling Lines, with our proprietary Closed Transfer Technology, will allow drug producers to offer consistent quality and effectiveness of injectable medicine, pharmaceuticals and vaccines at the highest safety level and lowest cost,” said Dr. Daniel Py, founder and CEO of MEDinstill.
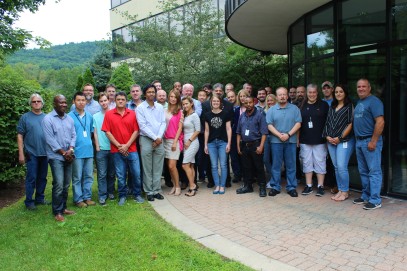
The MEDinstill team of 39 engineers, microbiologists and technicians have worked closely with the FDA over the past 15 years to deliver a completely closed transfer filling system that’s truly sterile.
In effect, the company said they have made obsolete the need for pharmaceutical companies to manufacture their products in large isolated environments.
“One manufacturing line can cost millions for a pharmaceutical company to set up and manufacture a vaccine where the potential for contamination is still possible. If these companies use our sterile INTACT Filling Lines, their investment cost can be reduced substantially,” said Debashis Sahoo, president of MEDinstill Development, a subsidiary.
Andreas Toba, chief medical manufacturing officer, added, “this is because the INTACT containers and filling heads are closed before, during and after filling.”
MEDinstill’s self-contained filling lines are modular, each sterile unit can be adapted to a client’s unique needs, and a conveyer line for packaging products can be added.
The smallest size is a desktop unit, which is used for labs and small volume testing. The standard INTACT filling terminal for a production line is nine feet long and six feet wide, which can be extended.
As for early adopters, “many of the pharmaceutical companies have expressed interest globally,” said Sahoo.
Pharmaceutical companies – or any company that requires a liquid product to be sterile – can also buy the system outright and install it at their facility.
Encube Ethicals in India already uses INTACT filling lines. “They were approved with the Indian FDA and manufacture lotions and creams that are truly preservative-free. This company is one of the largest manufacturers in the world for skincare products,” said Sahoo.

Now, MEDinstill plans to manufacture and package their own sterile IV bags with 0.9% saline injectable. These will be sold either directly to hospitals or to individual patients.
For many years, saline has been consistently on the FDA drug shortage list. Many patients in critical condition need liquid medications at bedside, which requires sterile saline.
MEDinstill is also in the final stage of developing a sterile Multidose Needleless Injector.
“This vital, lifesaving invention could potentially save humanity from a new pandemic flu virus or bioterrorist attack,” said Dr. Py.
“We can deliver 100 doses of vaccine out of the same IV bag via the multidose injector with no cross-contamination between patients and nurses in harsh environments,” said Sahoo.
Today’s needleless technology is limited to single use cartridges. Now, INTACT technology will allow 100 sterile doses delivered instead of one.
“This will set an unprecedented industry benchmark and we’ll achieve ‘just-in-time response’ to emergencies,” said Dr. Py.
“What we’re doing addresses what Bill Gates calls the biggest health and national security threat, which is the inability to respond just-in-time to deadly virus pandemics. This will be our legacy,” he added.
In addition, MEDinstill is laying the foundation for New Milford to become the epicenter of a brand-new industry.
“The revenue and job potential are huge, especially for Connecticut and the Housatonic River Valley. While many companies are struggling, MEDinstill is growing. It’s a revolution – especially for the pharmaceutical, biopharma and hospital industries,” stated David Gronbach, regulatory consultant for MEDinstill and former New Milford mayor.
Another major initiative is to create the Center of Excellence for sterile manufacturing of products. “MEDinstill customers who buy INTACT filling lines, FDA investigators that audit these lines, state licensing boards and non-government organizations could be trained in the new technology at our center in New Milford,” said Dr. Py.
Within the community, the company also plans to train and certify hospital staff and first responders – like how to operate machinery and administer vaccines – to better prepare for the next disaster.

“MEDinstill’s proprietary advanced technology for developing and manufacturing anti-contamination products, using closed transfer technology, is one component of our High-Tech Jobs & Training initiative. This will put New Milford on the map as we partner with the INTACT Valley Project, which I plan to fully support by collaboration with business, education and government communities,” said Mayor Pete Bass.
MEDinstill has already licensed the first-generation Sterile Filling Technology to GlaxoSmithKline for use with vaccines and then to Nestlé for the filling and delivery of sterile infant formula.
The company has filed more than 600 US and international patents related to sterile manufacturing and dispensing pharmaceutical drugs and sterile infant formula for premature babies.
Prior to forming MEDinstill, Dr. Py served as Merck’s medical director and director of research. He was responsible for ophthalmic product development and invented the artificial cornea that initially enabled 28 blind patients to regain their sight.
He holds an MD from Nancy University – with a specialty in ophthalmic surgery – and an ScD in Physics from the Institut National Polytechnique in Nancy, France.
Dr. Py, a longtime Bridgewater resident, said his life has come full circle since he was a surgeon, decades ago, at Nancy Hospital in his native France.
“On my first assignment, the professor of surgery told me to scrub all of the handles and determine the degree of contamination of the handles in the surgery area. Guess what? We found a lot! It’s all about hospital infection and the germs in hospital surgical centers, or anywhere, are unbelievable.”
“My life, and everything that I have accomplished in it, is my predestination. It’s a war against the germs,” said Dr. Py.
In Short Supply
“Drug shortages can occur for many reasons including manufacturing and quality problems, delays, and discontinuations. Manufacturers provide the FDA with most drug shortage information, and the agency works closely with them to prevent or reduce the impact of a shortage.” – FDA.gov
Did You Know?
According to the Center for Disease Control and Prevention, over 30,000 patients in U.S. hospitals die every year due to catheter-related bloodstream infections. The loss of life is completely preventable.
A shorter version of this feature originally appeared in the business section of a regional Connecticut newspaper in mid-June.
Article and photos: Alicia Sakal
If you’d like to read more stories like this one, then please like / follow Candlewood Lake Magazine on Facebook.